Pigments for Masterbatch & Plastics Applications
- Share
- Issue Time
- Jul 15,2023
Summary
Introduction about Application of Organic Pigments in Masterbatch & Plastics
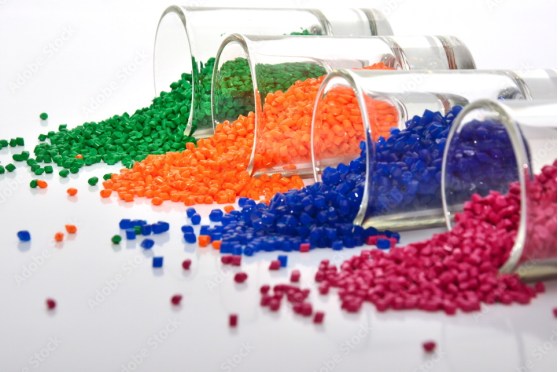
Properties of Performance Pigments for Plastic.
Weather / Aging
Effects of sunlight on plastic products:
sunlight exposure and some artificial lights can have adverse effects on the usefulness of plastic products. So polymers used outdoors normally
require UV protection and weather resistant pigments.
The light stabilizing system must be considered together with the pigment formulation and the fastness criteria specified for the final product.
Light fastness
Light Fastness is a measure of the color fastness of a plastic article when used in indoor applications (UV light exposure without direct Water contact) If a pigment has good Light Fastness, it does not always mean that it has good weather fastness.
Pigment selection for plastics used in indoor applications depends on certain factors, such as:
o Polymer type
o Concentration of the pigment
o Presence of titanium dioxide (which typically accelerates fading)
o Required Light Fastness
o Service conditions
Pigment performance can also be influenced by surface of the article, processing heat history and stabilization package. Generally, inorganic pigments exhibit superior light fastness than organics. Tables below rank light fastness of main families of organic pigments.
Warping / Nucleation
The degree of crystallinity and the speed of crystallization determine the final properties of a plastic article. Organic pigments are known to influence these parameters during the cooling phase of plastic processing, particularly in HDPE injection molding.
This can result in:
o Reduced mechanical stability
o Impact on dimensional stability
o Warping
o Shrinkage
Typical applications where this effect becomes important are containers, crates, and caps & closures. Pigments can be divided into three groups, depending on their influence on the shrinkage of HDPE injection molding systems.
Transparency
Usually, transparency is obtained by reducing pigment particle size as possible. This is achieved by surrounding the particles as soon as they are formed with a coating, which prevents the growth of crystals. The most common products used for this coating are rosin or rosin derivatives. This is particularly useful for printing ink pigments that are required to have high transparency and it has the added advantage that such pigments are more easily dispersed.
Iron oxide pigments can be opaque or transparent. The transparent variety are an important group of inorganic pigments as they are widely used for metallic finishes, where their high level of transparency gives an attractive finish, and their weatherability resistance improves the weatherability of pigments with which they can be combined. This is known as a synergistic effect. Transparent iron oxides depend on the particles being unusually small, and also having a crystal shape.
o Effect of Dispersion on Transparency - The dispersion process can influence transparency, as it involves breaking up agglomerates of particles to individual primary particles. However, primary particles are not split up by the dispersion process. All one can do is to make full use of the pigments original particle size. Good dispersion will maximize the transparency of a small particle.
o Measurement of transparency - Transparency is simply assessed by applying the coating over a black and white contrast chart and measuring the color difference. The greater the color difference, the higher the transparency.
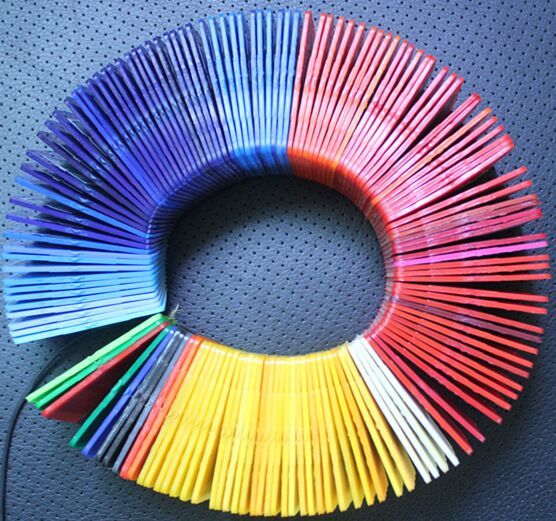